Estimated reading time: 9 minutes
Key Takeaways
- Diverse Design Styles: Laser cutting accommodates various styles like geometric, mandalas, typographic, nature-inspired, and 3D layered designs, allowing for versatile artistic expression.
- Material Matters: Choosing the right wood (e.g., Baltic Birch Plywood, MDF, Basswood, Cherry, Walnut) significantly impacts cutting quality, aesthetic, and project suitability.
- Optimize Settings & Techniques: Achieving perfect cuts requires adjusting laser power, speed, and frequency, along with crucial techniques like test cuts, air assist, pre-masking, sanding, painting, staining, and sealing.
- Project Versatility & Personalization: Laser cutting is ideal for a wide range of projects, from custom coasters and ornamental boxes to personalized signs and intricate home decor, with ample opportunities for customization and unique DIY gifts.
- Design File Management: Sourcing or creating appropriate vector design files (SVG, DXF, AI) is essential, and building a personal design library can foster creativity and efficiency.
Discover the world of laser cut wood designs, a versatile method for crafting everything from intricate art pieces to personalized gifts. This guide will walk you through popular design ideas, material considerations, and tips for achieving stunning results with your laser cutter, inspiring your next woodworking project.
Exploring Popular Laser Cut Wood Design Styles
The journey to a stunning laser cut wood design often begins with a pivotal decision: selecting a design style. This choice acts as the creative compass for your project, influencing everything from the intricacy of the cut to the final aesthetic appeal. Creative laser cut projects don’t just happen; they are born from a clear vision, and a well-defined style is the cornerstone of that vision. The beauty of laser cutting lies in its ability to transform a humble piece of wood into an extraordinary object through the application of precise and often breathtaking intricate wood laser patterns. Let’s delve into some of the most popular styles that can serve as inspiration for your next creation.
- Geometric Patterns: The allure of geometric designs lies in their versatility and timeless appeal. From minimalist grids and chevrons to complex tessellations and fractal-like structures, these patterns rely on symmetry, repetition, and the interplay of positive and negative space. Intricate wood laser patterns in geometric forms can create dynamic visual effects, suggesting movement, depth, or even optical illusions. They are equally at home in contemporary décor, adding a sleek, modern touch, as they are in more traditional settings when employing classic motifs like Art Deco borders or Islamic geometric art. The precision of laser cutting allows for sharp lines and perfect angles, making geometric styles exceptionally crisp and impactful.
- Intricate Mandalas: Mandalas, with their spiritual origins in Hinduism and Buddhism, are circular designs symbolizing the universe and promoting meditation. Laser cutting is exceptionally well-suited for rendering the delicate symmetry and layered details characteristic of mandalas. These intricate wood laser patterns can transform a simple wooden disc into a captivating piece of laser cut wood art. They are popular for wall hangings, coasters, jewelry pendants, or as central decorative elements in larger compositions. The laser’s ability to execute extremely fine cutouts and etchings means even the most complex mandala, rich with symbolic layers, can be reproduced with stunning fidelity, turning wood into a canvas for spiritual or purely aesthetic expression.
- Typographic Art: Words have power, and typographic art harnesses this by treating letters and text as visual elements. Laser cutting enables the creation of crisp, precise letterforms, from flowing, delicate scripts to bold, impactful sans-serifs. This style is perfect for personalized DIY laser cut wood gifts, such as custom name signs for nurseries, monogrammed keepsake boxes, or plaques featuring favorite quotes or poems. Beyond simple text, typographic art can involve arranging words into significant shapes (e.g., a love poem in the shape of a heart), creating interlocking letter designs, or integrating text with imagery for a more complex piece of laser cut wood art. The choice of font, weight, spacing (kerning), and layout are crucial in conveying the desired tone and aesthetic, making each typographic piece unique.
- Nature-Inspired Motifs: Bringing the outdoors in, nature-inspired motifs remain a perennial favorite for laser cut wood designs. This broad category includes everything from detailed representations of leaves, flowers, trees, and animal silhouettes to more stylized or abstract interpretations of natural forms. The organic shapes and flowing lines inherent in these designs provide a beautiful contrast to the often geometric nature of man-made objects. Intricate wood laser patterns can capture the delicate veins of a leaf, the majestic spread of a tree’s branches, or the intricate details of an animal’s fur or feathers. These motifs are ideal for creating themed décor for homes or events, personalized gifts for nature lovers, or adding a touch of warmth and serenity to any space. Think of woodland scenes, botanical illustrations, or stylized animal portraits.
- 3D Layered Designs: For those looking to add literal depth and dimension to their work, 3D layered designs offer a fascinating avenue for creative laser cut projects. This technique involves cutting multiple layers of wood, each with different elements of the overall design, and then stacking and adhering them to create a three-dimensional effect. The interplay of light and shadow across the layers significantly enhances the visual impact and complexity. Common examples include intricate shadow boxes depicting detailed scenes, multi-layered maps showcasing topographical features or cityscapes, or abstract sculptural forms. Carefully planned intricate wood laser patterns on each individual layer contribute to the cumulative richness of the final piece. Varying wood types, stains, or paints on different layers can further accentuate the depth and draw attention to specific elements within the design.
Finding or creating the right laser cutting design files is essential to successfully executing any of these styles. Numerous online marketplaces, design communities, and repositories offer a vast array of pre-made files suitable for laser cutting, typically in vector formats like SVG, DXF, or AI. Alternatively, for those with a specific vision or a desire for complete originality, design software such as Adobe Illustrator, CorelDRAW, or Inkscape allows for the creation of entirely custom patterns from scratch, though this requires a different set of skills that are often developed over time.
Choosing a style isn’t just about pure aesthetics; it’s about thoughtfully aligning the design with the project’s intended purpose, the characteristics of the wood itself, and the recipient’s taste, especially when crafting DIY laser cut wood gifts. A playful animal silhouette or a nature-inspired design might be perfect for a child’s room décor, while an elegant mandala or a sophisticated geometric pattern could serve as striking laser cut wood art in a living space or office. Consider the complexity you’re comfortable working with, not only in terms of the design file itself but also for any post-cutting assembly, as is common with 3D layered designs. The selected style should not only inspire you but also resonate with the intended function or message of your creative laser cut project, ensuring the intricate wood laser patterns effectively elevate the final piece from a simple piece of wood to a cherished work of art or a meaningful gift.
Materials and Techniques for Perfect Wood Cuts
Once your design style is chosen, the next critical step towards realizing your laser cut wood designs is selecting the right material and mastering the techniques for a perfect cut. The type of wood you choose dramatically influences not only the final aesthetic but also how easily and cleanly your intricate wood laser patterns will render. Different woods react differently to the laser beam, and understanding these nuances is key to success.
Choosing Your Wood: Pros and Cons
The market offers a variety of woods suitable for laser cutting, each with its unique characteristics:
- Plywood: A popular choice, especially Baltic Birch Plywood, due to its stability, relative affordability, and consistent thickness. It’s excellent for structural projects and larger decorative pieces.
- Pros: Good strength-to-weight ratio, available in various thicknesses and veneer finishes. Birch plywood often has a light, even grain that engraves well.
- Cons: The glue layers within plywood can sometimes be inconsistent or harder than the wood itself, leading to uneven cutting or increased charring. Lower-grade plywoods may contain voids which can disrupt intricate wood laser patterns. The cut edges will show the layers, which can be a desirable or undesirable aesthetic.
- MDF (Medium-Density Fiberboard): An engineered wood product made by breaking down hardwood or softwood residuals into wood fibers, combining them with wax and a resin binder, and forming panels by applying high temperature and pressure.
- Pros: Extremely uniform density, resulting in very consistent cuts and engravings with minimal charring. Its smooth surface is ideal for painting, making it a favorite for colorful laser cut wood art or projects where the natural wood grain isn’t desired. It’s often more affordable than quality solid woods.
- Cons: Not as visually appealing in its raw state as natural wood. The dust produced during cutting is very fine and can be more of a nuisance. It’s also heavier than most plywoods and solid woods of similar thickness and doesn’t hold screws as well.
- Solid Woods: Offer a premium look and feel, with each species bringing its own color, grain, and cutting properties.
- Basswood: A very soft, lightweight hardwood with a fine, even texture. It cuts exceptionally well with low laser power, producing minimal charring. Ideal for highly detailed engravings and delicate intricate wood laser patterns, perfect for models or intricate DIY laser cut wood gifts.
- Cherry: Valued for its rich reddish-brown color that deepens with age and its smooth grain. It cuts and engraves beautifully, though it requires more power than basswood. Can sometimes have small resinous pockets that might flare up.
- Walnut: A stunning dark, rich hardwood. It cuts cleanly and engraves with excellent contrast. Being harder, it requires more laser power or slower speeds than cherry or basswood. Excellent for high-end laser cut wood art and premium gifts.
- Pros (General): Unmatched natural beauty and aesthetic appeal of real wood grain.
- Cons (General): More expensive than plywood or MDF. Can be prone to warping or cupping, especially thinner sheets. Grain direction can influence the strength of delicate cut parts and may sometimes cause slight variations in cut depth.
The choice of material directly affects how intricate wood laser patterns manifest. Denser woods or those with inconsistent glue layers (like some plywoods) may require more power or slower speeds, potentially leading to more noticeable charring on delicate details. Softer, uniform woods like Basswood or MDF are often preferred for highly detailed work as they allow for finer lines and less heat buildup.
Optimizing Laser Cutter Settings
Achieving clean cuts and sharp details hinges on correctly configuring your laser cutter’s power, speed, and frequency (often expressed as PPI – Pulses Per Inch). There’s no one-size-fits-all setting; these parameters must be adjusted based on the wood type, its thickness, and your specific laser machine.
- Power: Too low, and the laser won’t cut through; too high, and you’ll get excessive burning, charring, and a wider kerf (the width of the material removed by the laser).
- Speed: Too fast, and the cut may not be complete; too slow, and it leads to overburning and charring, especially on delicate parts of intricate wood laser patterns.
- Frequency/PPI: For wood, a higher PPI (e.g., 500-1000) generally results in a smoother edge, almost like a continuous burn. Lower PPI can sometimes reduce charring on certain materials but might leave a more perforated edge.
Always perform test cuts on a scrap piece of the same material before running your final design. Create a small test grid with varying power and speed settings to find the sweet spot for your chosen wood. Proper air assist is also crucial; a strong, focused stream of air directed at the cutting point helps to clear debris, reduce flaming, and minimize charring, leading to cleaner cuts.
Finishing Techniques for Polished Results
Once your design is cut, finishing techniques can elevate your laser cut wood art or DIY laser cut wood gifts from good to exceptional.
- Cleaning and Sanding: Smoke residue or “halos” around cut edges are common. Pre-masking the wood surface with painter’s tape or specialized laser masking material before cutting is a highly effective technique to prevent these stains on the top surface, drastically reducing cleanup. If masking wasn’t used, or for cleaning cut edges, gentle sanding with fine-grit sandpaper (e.g., 220 grit or higher) can remove char and smooth edges. Be cautious with very delicate intricate wood laser patterns. A soft brush or compressed air can remove sanding dust.
- Painting: MDF is particularly well-suited for painting due to its smooth, uniform surface. Apply a primer first for best results, followed by acrylics, spray paints, or other wood paints. Multiple light coats are better than one heavy coat.
- Staining: Stains enhance the natural grain of woods like Baltic Birch Plywood, Cherry, or Walnut. Apply evenly with a cloth or brush, and wipe off excess according to the stain manufacturer’s instructions. Always test stains on a scrap piece first, as the final color can vary.
- Sealing: Applying a clear sealant (varnish, lacquer, or polyurethane) protects the wood from moisture and wear, and can add a desired sheen (matte, satin, or gloss). This is especially important for items that will be handled frequently or exposed to varying humidity.
Finally, when sourcing laser cutting design files, especially for projects involving interlocking parts or specific thicknesses, try to find files that specify recommended material types or provide versions for different material thicknesses. This forethought in the design stage can save considerable adjustment time later. By carefully selecting your materials and mastering these cutting and finishing techniques, you’ll be well-equipped to transform your creative visions into beautifully executed laser cut wood pieces.
Bringing Your Laser Cut Wood Designs to Life Projects and Inspiration
With a solid understanding of design styles, materials, and cutting techniques, you’re now poised to bring your laser cut wood designs to life. The true magic happens when you transform a concept and a piece of wood into a tangible object, whether it’s a piece of statement laser cut wood art or a heartfelt DIY laser cut wood gift. The possibilities are as boundless as your imagination, so let’s explore some inspiring project ideas and discuss how you can embark on your own creative laser cut projects.
Inspiring Project Examples
The versatility of laser cutting lends itself to a myriad of applications. Here are a few popular project ideas to spark your creativity:
- Custom Coasters: Often a beginner-friendly project, coasters are incredibly versatile. You can etch them with intricate mandalas, geometric patterns, monograms, or even tiny landscapes. These make fantastic personalized DIY laser cut wood gifts and are a staple in the ‘Coaster‘ product category on design file marketplaces. Imagine a set featuring local landmarks or inside jokes!
- Ornamental Boxes: Laser cutting allows for the creation of beautiful and functional boxes with intricate fretwork, inlay effects (simulated or actual), or detailed engravings. These can range from small jewelry boxes to larger keepsake containers. Many designs for such items can be found in the ‘Boxes‘ product category and often feature clever joinery like living hinges or finger joints, all achievable with laser precision. The lid itself can become a canvas for stunning intricate wood laser patterns.
- Personalized Signs: Custom signage is a hugely popular application. Think welcome signs for homes, name plaques for children’s rooms (a common find in the ‘Signs‘ product category), inspirational quote art for an office, or even branded signage for small businesses. Typography, silhouettes, and borders all play a significant role here, and laser cutting ensures crisp, professional results.
- Unique Home Decor Items: Beyond signs and boxes, consider creating more elaborate decorative pieces.
- Candle Lanterns: Panels with intricate cutouts depicting nature scenes, geometric patterns, or even abstract designs can be assembled into beautiful lanterns that cast enchanting shadows.
- Picture Frames: Elevate a simple picture frame by engraving it with meaningful dates or names, or by laser cutting an ornate overlay to sit atop a standard frame.
- Wall Art Panels: Large-scale laser cut wood art panels featuring layered designs, complex geometric patterns, or nature-inspired motifs can become stunning focal points in a room.
Developing Your Own Creative Laser Cut Projects
While pre-made laser cutting design files are a fantastic starting point, the real joy often comes from making something uniquely yours. Don’t be afraid to adapt or customize existing designs. This could be as simple as adding a name or date to a template, resizing elements, or combining parts from different designs. For instance, you might take a floral element from one pattern and integrate it into a border for a frame design. Software like Adobe Illustrator, Inkscape, or LightBurn allows you to modify vector files, giving you the power to tweak, merge, and personalize.
To truly foster your own creative laser cut projects, consider starting with a specific purpose or recipient in mind for DIY laser cut wood gifts. What are their interests? What colors or styles do they prefer? This personal connection can fuel incredible design ideas. For laser cut wood art, let your personal aesthetic guide you. What moves you? What kind of atmosphere do you want to create?
Finding Inspiration and Building Your Design Library
Inspiration for intricate wood laser patterns is all around you. Look to nature for organic shapes and textures, explore architectural details, delve into historical textile patterns, or browse online platforms like Pinterest, Etsy (for finished product ideas), and dedicated design repositories. Many designers share or sell laser cutting design files that can be a great source of inspiration, even if you intend to create your own. Start a digital (or physical) mood board to collect images, patterns, and color schemes that resonate with you.
Consider how elements from seemingly unrelated inspirations can be combined. For example, an elegant filigree pattern from an ‘Ornaments‘ product category could be adapted to create stunning detailing on a keepsake box. A design intended for a ‘3D illusion‘ lamp could be re-imagined as a layered wall art piece. Building your own library of design elements—favorite flourishes, borders, or base shapes—can speed up your workflow and help you develop a signature style. The journey from inspiration to a beautifully finished laser cut wood design is incredibly rewarding, transforming simple materials into objects of beauty and meaning.
Conclusions
Laser cutting opens endless possibilities for wood designs. By exploring diverse styles, understanding material nuances, and using the right design files, you can create truly unique items. We hope this guide has sparked your imagination and equipped you to embark on exciting laser cut wood projects.
FAQ
Q: What are the most popular design styles for laser cut wood?
A: Popular design styles include Geometric Patterns, Intricate Mandalas, Typographic Art, Nature-Inspired Motifs, and 3D Layered Designs. Each offers unique aesthetic possibilities, from modern sleekness to spiritual symbolism or intricate depth.
Q: Which types of wood are best for laser cutting, and what are their pros and cons?
A: Common woods for laser cutting include Plywood (like Baltic Birch, stable and affordable but can char unevenly), MDF (uniform, great for painting, but heavy and not visually appealing raw), and Solid Woods like Basswood (soft, minimal charring), Cherry (rich color, engraves beautifully), and Walnut (dark, clean cuts, excellent contrast). Solid woods offer natural beauty but are more expensive and prone to warping.
Q: How can I prevent charring and achieve clean cuts with a laser cutter?
A: To prevent charring and achieve clean cuts, optimize your laser cutter’s settings (power, speed, frequency) based on the wood type and thickness. Always perform test cuts, use proper air assist to clear debris, and consider pre-masking the wood surface with tape to protect against smoke residue.
Q: What finishing techniques can I use to enhance my laser cut wood projects?
A: After cutting, you can clean and sand the edges to remove char. Painting (especially good for MDF), staining (to enhance natural grain), and sealing (with varnish, lacquer, or polyurethane) can elevate your projects, adding protection and a desired sheen.
Q: Where can I find or create laser cutting design files?
A: You can find pre-made laser cutting design files in vector formats (SVG, DXF, AI) on online marketplaces, design communities, and repositories. For custom designs, you can use software like Adobe Illustrator, CorelDRAW, or Inkscape to create your own patterns from scratch.
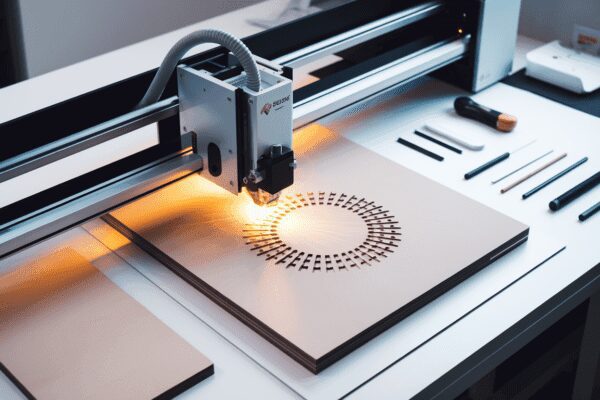
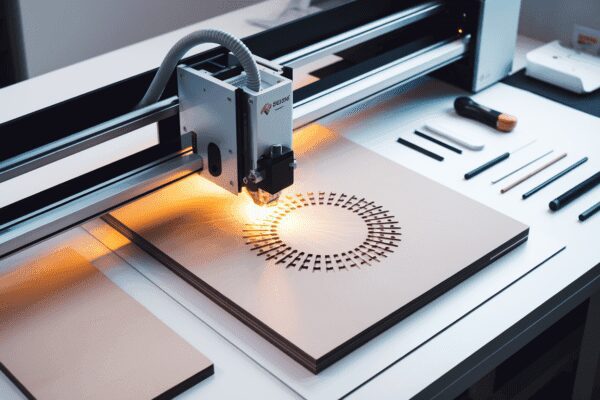
Subscribe to Our Newsletter
And enjoy FREE Download Files, SALE Alerts and Inspiring TIPS
How to Create Stunning Engraved Slate Coasters
How to Create Stunning Engraved Slate Coasters
A Guide to Creating the Perfect Engraved Charcuterie Board
[Free Download] Wild Bear Chef Charcuterie Board Engraving File | PNG …
$6.00Original price was: $6.00.$0.00Current price is: $0.00.Free Download
[Free Download] Tiger Chef 3D Illusion Charcuterie Board Engraving | P…
$6.00Original price was: $6.00.$0.00Current price is: $0.00.Free Download
Valentine Love Captions: 6 Charcuterie Board Engraving Files…
$12.00Original price was: $12.00.$7.20Current price is: $7.20.(40% off)
American Eagle Flag Laser Engraving File for Charcuterie & Cutting…
$6.00Original price was: $6.00.$3.90Current price is: $3.90.(35% off)