To ensure your laser engraver operates at peak efficiency and delivers consistent, high-quality results, regular maintenance is crucial. This guide will walk you through essential practices, from routine cleaning to in-depth troubleshooting, helping you extend the lifespan of your machine and maintain optimal performance for all your engraving projects.
Estimated Reading Time: 13 minutes
Key Takeaways
- Regular laser engraver maintenance is crucial for machine longevity, precision, and consistent high-quality output, preventing costly repairs and downtime.
- Meticulous cleaning of optical components (lenses, mirrors) is paramount, requiring specialized tools and techniques to ensure optimal laser beam quality and power delivery.
- Proper mechanical maintenance, including lubrication of moving parts, precise alignment of laser mirrors, and routine inspection of belts and pulleys, ensures accurate and smooth laser head movement.
- Optimizing laser performance involves continuous calibration of settings for different materials and consideration of environmental factors like temperature and humidity.
- A systematic approach to troubleshooting, starting with optical and mechanical checks, enables users to quickly diagnose and resolve common engraving issues.
Table of Contents
- Understanding the Importance of Regular Laser Engraver Maintenance
- Essential Cleaning Protocols for Your Laser Engraver
- Mechanical Maintenance: Lubrication, Alignment, and Inspection
- Advanced Tips for Optimizing Laser Performance and Troubleshooting Common Issues
- Conclusions
Understanding the Importance of Regular Laser Engraver Maintenance
Consistent maintenance is not merely a suggestion for laser engravers; it is an absolute imperative for anyone serious about maximizing their machine’s potential and safeguarding their investment. Without a dedicated routine of care, the intricate interplay of optical, mechanical, and electrical components within a laser engraver will inevitably degrade, leading to a cascade of negative effects that impact everything from output quality to operational costs. This chapter delves into the fundamental reasons why diligent maintenance is so critical, exploring its profound impact on machine longevity, accuracy, and overall performance.
The most immediate benefit of regular maintenance is its direct contribution to the longevity of your laser engraver. Like any precision instrument, a laser machine is designed with specific tolerances and operational parameters. Over time, internal components accumulate dust, debris, and residues from engraving processes. Lenses and mirrors can become smudged or pitted, leading to reduced laser power transmission and uneven engraving. Bearings and guides can become dirty or unlubricated, introducing friction and wear that accelerate component fatigue. Neglecting these seemingly minor issues allows them to compound, forcing critical parts to work harder and less efficiently, ultimately shortening their operational lifespan significantly. A maintained machine experiences less stress on its parts, leading to fewer unexpected breakdowns and a considerably longer operational life, thereby deferring the costly expense of replacement.
Beyond mere survival, proper maintenance is the cornerstone of maintaining a laser engraver’s accuracy and precision, which are paramount for producing high-quality work. The laser beam itself is exceptionally precise, but its effectiveness is entirely dependent on the integrity of the optical path. Dust particles on lenses and mirrors scatter the laser light, reducing its focus and intensity, resulting in fuzzy engravings, incomplete cuts, and inconsistent etching depths. Misaligned mirrors, often caused by vibrations or loosened fasteners over time, can lead to the laser beam striking the work surface at an incorrect angle, causing distortion and reduced power. Similarly, neglected mechanical components like linear rails and belts can introduce backlash or inconsistent motion, resulting in skewed designs or inaccurate positioning. Consistent cleaning of optics ensures optimal beam quality, while regular checks of mechanical alignments guarantee the machine moves exactly as commanded, preserving the fine detail and accurate dimensions essential for professional results.
The correlation between proper care and optimizing laser performance cannot be overstated. A well-maintained machine operates at its peak efficiency, delivering consistent power, precise movement, and superior results every time. This translates directly into higher productivity and less material waste. When the machine performs optimally, jobs are completed faster, rework is minimized, and the quality of the output consistently meets or exceeds expectations. Conversely, a poorly maintained machine will struggle, requiring more passes to achieve desired results, consuming more power, and often failing to meet quality standards, leading to wasted time, materials, and ultimately, frustrated operators. Preventative measures, such as routine cleaning of internal components, checking for loose connections, and lubricating moving parts, are proactive steps that avert major problems. These small, consistent efforts prevent the snowball effect of minor issues escalating into significant, costly repairs or debilitating downtime. For example, a few minutes spent cleaning optics can prevent hours of troubleshooting an apparent drop in laser power, or a quick check of belt tension can prevent a complete halt in production due to a thrown belt. This proactive approach saves not only money in repair costs and material waste but also invaluable time that would otherwise be spent on reactive fixes and delayed projects.
Ultimately, regularity in maintenance is the true key to unlocking and maintaining the full potential of any laser engraving machine. It allows the machine to operate within its designed parameters, ensuring consistent functionality, reliable output, and maximum uptime. It safeguards the investment made in the equipment, extends its usable life, and ensures that it remains a reliable tool for high-quality production for years to come. Ignoring maintenance is akin to expecting a high-performance vehicle to run flawlessly without oil changes or tire rotations; eventually, it will break down, and the cost of repair or replacement will far outweigh the minor effort of consistent upkeep. Embracing a proactive maintenance mindset transforms the laser engraver from a temperamental tool into a dependable workhorse, consistently delivering precision and performance.
Essential Cleaning Protocols for Your Laser Engraver
Having understood the overarching importance of regular maintenance, the practical application of this principle primarily begins with meticulous cleaning. While the previous chapter highlighted how neglect impacts machine longevity and accuracy, this section will delve into the specific, critical cleaning procedures necessary for a laser engraver. The emphasis here is on precision cleaning, particularly for the delicate optical components, as their pristine condition is paramount to achieving and maintaining optimal laser performance and impeccable engraving quality.
The single most crucial aspect of laser engraver cleaning revolves around its optical components, chief among them being the mirror and cleaning laser lens. These elements are directly responsible for guiding and focusing the laser beam onto the material. Even a microscopic speck of dust, a fingerprint, or a residue film on these surfaces can scatter or absorb laser energy, leading to a significant reduction in beam intensity, uneven engraving, or even permanent damage to the optics due to localized overheating. For these reasons, cleaning these components demands extreme care and the right tools.
Cleaning Optical Components: Lenses and Mirrors
Before handling any optical component, ensure your machine is powered off and cooled down. Always wear clean, lint-free gloves to prevent transferring skin oils to the delicate surfaces. Begin by using a can of compressed air (designed for electronics, not general purpose industrial air) to gently blow away any loose dust or debris. Hold the can upright and at a distance to avoid propellant residue. Never use shop air, as it often contains oil and moisture.
For more stubborn contaminants like residue or smudges, specialized lens cleaning solutions and lint-free lens tissues or optical-grade cotton swabs are essential. Isopropyl alcohol (99% pure electronic grade) or specific optical cleaning solutions recommended by your engraver’s manufacturer are generally safe. Apply a small amount of the solution to the lint-free tissue or swab, never directly to the lens or mirror. Gently wipe the surface in a single, smooth stroke from the center outwards, rotating the tissue or using a fresh side for each wipe until the surface is clear. Avoid circular motions or excessive pressure, as this can scratch the delicate coatings. For recessed lenses, like those found in the laser head, a specialized long-handled swab might be necessary. It is crucial to have a dedicated cleaning kit for optics and to keep all cleaning materials meticulously clean and dust-free. The frequency of optical cleaning depends heavily on usage and the type of materials being engraved; highly dusty or resinous materials will necessitate more frequent cleaning. Diligent cleaning directly influences the quality of engraving output by ensuring the laser beam remains perfectly focused and consistently powerful, resulting in sharp lines, precise cuts, and uniform etching.
Exhaust System and Work Area Cleaning
Beyond the delicate optics, the exhaust system and the general work area also require consistent attention. The exhaust system – comprising the fan, ducting, and possibly a filter – is vital for removing smoke, fumes, and particulate matter generated during the engraving process. Over time, these contaminants build up as greasy, sticky residues within the system, reducing airflow efficiency and potentially becoming fire hazards. A clogged exhaust system means poor fume extraction, leading to smoke accumulation inside the machine (which then quickly contaminates optics) and poor air quality in the workspace. Regularly inspect and clean the exhaust fan blades and the inside of the ducting. Depending on the build-up, this might involve simply wiping with a damp cloth or, for heavy resinous deposits, using a mild degreaser, ensuring it’s compatible with the ducting material. Replace or clean filters as per manufacturer guidelines; a saturated filter significantly impedes airflow.
The work area, including the honeycomb bed or slat bed, accumulates debris, small cut pieces, and charring. This debris can interfere with material placement, cause uneven engraving due to uneven support, and even reflect laser energy back onto the material or the machine, risking damage. Regularly vacuum the work bed, and for stubborn char marks or residues, a brass brush or specialized cleaning tool can be used. Some honeycomb beds can even be soaked in a degreasing solution or pressure washed (ensure they are thoroughly dried before reinstallation). Cleaning the general enclosure of the engraver, wiping down the interior surfaces, and clearing any dust from mechanical rails and belts prevents dust from migrating back to critical components. A clean work environment significantly contributes to efficient operation, prolongs the machine’s life by preventing debris-related wear and contamination, and is a foundational element in ensuring consistent, high-quality engraving output.
Mechanical Maintenance: Lubrication, Alignment, and Inspection
While optical cleanliness is foundational, the mechanical integrity of your laser engraver is equally vital for consistent performance, precision, and longevity. The moving parts of the machine, responsible for accurately positioning the laser head across the work area, are subject to wear and tear. Proper mechanical maintenance ensures these components operate smoothly, quietly, and precisely, directly translating into stable laser engraving performance and preventing a host of common issues. This chapter provides a comprehensive guide to these mechanical aspects, focusing on lubrication, alignment, and routine inspection.
Lubrication of Moving Parts
Smooth motion is paramount for precise engraving and cutting. The gantry system, which includes linear rails, bearings, and lead screws, facilitates the precise movement of the laser head. Over time, friction, dust, and debris can impede this movement, leading to jerky operation, inaccurate positioning, and premature wear of components. Therefore, lubricating laser rails and other moving parts is an essential preventative measure.
Before applying lubricant, always clean the rails thoroughly. Use a lint-free cloth dampened with isopropyl alcohol or a mild degreaser to wipe away any accumulated dust, old grease, or residue. Once clean and dry, apply a thin, even layer of a specialized lubricant designed for linear motion systems. Many manufacturers recommend specific types of light machine oil, lithium grease, or silicone-based lubricants. Avoid using general-purpose oils like WD-40, as they can attract dust and eventually gum up the mechanisms. Apply a few drops or a small bead of lubricant to each rail, then manually move the laser head back and forth along the full length of the axis several times to distribute the lubricant evenly. Pay particular attention to the bearing blocks that slide along the rails. If your machine uses lead screws, apply a similar lubricant to the threads. This lubrication reduces friction, extends the lifespan of the bearings and rails, and ensures silent, effortless movement, which is critical for maintaining positional accuracy during engraving and cutting operations. The frequency of lubrication depends on usage and environmental factors, but a general guideline is every 100-200 hours of operation or monthly for heavy users.
Aligning Laser Mirrors
Following optical cleaning, the next critical step for maintaining laser beam accuracy and power delivery is the precise aligning of laser mirrors. Your laser engraver typically has several mirrors (usually two or three) that steer the laser beam from the laser tube, through the gantry system, and down into the focusing lens in the laser head. If these mirrors are even slightly out of alignment, the laser beam will not pass cleanly through the center of each mirror or enter the focusing lens axially, leading to significant power loss, an unfocused or distorted beam at the material surface, and uneven engraving or incomplete cuts. Misalignment can manifest as a weak spot in the beam, charring where it shouldn’t be, or inconsistent cut depths.
The alignment process is meticulous and requires patience and precision. It often involves firing short pulses (dot tests) of the laser at specific points to check the beam’s trajectory. The goal is to ensure the beam strikes the exact center of each subsequent mirror and passes centrally through the aperture of the focusing lens assembly, regardless of the laser head’s position within the work area. Adjustments are made using the small adjustment screws on the mirror mounts. It is crucial to follow your specific machine’s manual for the exact alignment procedure, as it can vary between models. If uncertain, consult a qualified technician. Proper alignment directly ensures that the maximum possible laser power reaches the material in a perfectly focused and consistent manner, which is fundamental to achieving high-quality, precise engraving and cutting results.
Inspection of Belts, Pulleys, and Connections
Regular inspection of the drive system components is a simple yet effective preventative measure against many common mechanical issues. The vast majority of consumer and light industrial laser engravers use timing belts and pulleys to translate motor rotation into linear motion. Over time, these belts can stretch, fray, or accumulate debris in their teeth, leading to backlash, skipped steps, or inconsistent movement. Pulleys can become loose or their teeth can wear down.
During your routine checks, visually inspect all belts for signs of wear such as cracks, fraying, or missing teeth. Gently feel the tension of each belt; it should be taut but not overly tight (which can strain motors and bearings). If a belt feels loose, consult your manual for the proper tensioning procedure. Check that all pulleys are securely fastened to their motor shafts and that idler pulleys spin freely and smoothly. Also, inspect all cable connections, particularly those going to the motors and limit switches, ensuring they are snug and free from damage. Loose connections can lead to intermittent operation, false readings, or complete failure of a component. These regular checks contribute significantly to stable laser engraving performance by ensuring that the laser head moves predictably and accurately, preventing issues like wavy lines, incorrect scaling, or missed engraving areas that can ruin a project and waste material. Adopting these mechanical maintenance habits will extend the operational life of your machine’s moving parts and ensure consistent, high-precision results.
Advanced Tips for Optimizing Laser Performance and Troubleshooting Common Issues
While consistent basic and mechanical maintenance forms the bedrock of a well-functioning laser engraver, true mastery involves understanding the subtle nuances of operation and being equipped to diagnose and resolve issues. This chapter transcends routine upkeep, offering advanced tips for optimizing laser performance through meticulous setting calibration and an understanding of environmental impacts. Furthermore, it provides a systematic approach to troubleshooting engraving issues, empowering users to effectively diagnose and resolve problems, ensuring the machine consistently performs at its peak.
Calibrating Settings and Environmental Considerations
Optimizing laser performance goes beyond simply having a clean and well-maintained machine; it involves finely tuning your settings to the specific material and environmental conditions. Even with a perfectly aligned and clean optical path, incorrect power, speed, or frequency settings can lead to suboptimal results. The “perfect” settings for a given material are rarely static. Factors such as the material’s exact composition, thickness, color, and even density can vary between batches. For instance, a sheet of 3mm birch plywood from one supplier might engrave differently than another. Therefore, it’s highly recommended to perform material testing or calibration tests for new batches or types of materials. These tests involve creating a grid of squares or lines, each engraved at slightly different power and speed settings, allowing you to visually identify the optimal combination for the desired effect (e.g., precise cutting, deep engraving, or light etching). Documenting these optimal settings in a logbook is an advanced practice that saves significant time and material in the long run.
Environmental factors, often overlooked, can also significantly impact laser performance. Temperature, in particular, plays a crucial role, especially for CO2 laser tubes. Most CO2 lasers perform optimally within a specific operating temperature range (typically 18-25°C or 65-77°F for the cooling water). If the cooling water is too warm, the laser tube’s power output can decrease, and its lifespan can be shortened. If it’s too cold, condensation can form inside the tube, potentially leading to arcing and damage. Monitoring your chiller’s temperature and ensuring it’s within the manufacturer’s recommended range is crucial. Humidity can also affect delicate optical components and lead to moisture absorption in certain materials, altering their engraving characteristics. Maintaining a stable, climate-controlled environment in your workshop can contribute significantly to consistent laser performance and product quality.
Troubleshooting Engraving Issues: A Systematic Approach
Despite diligent maintenance, issues can still arise. The key to effective troubleshooting is a systematic approach, starting with the most common and easily identifiable culprits.
Power Fluctuations or Weak Output: If your engraving is shallow or cuts are incomplete, despite using previously reliable settings, suspect power issues.
First Check: Optical Path Obstruction. Revisit “Essential Cleaning Protocols.” Is there dust or debris on any mirrors or lenses? Even a tiny speck can absorb significant power. Re-clean all optics.
Second Check: Mirror Alignment. Perform a laser alignment test. Even a slight misalignment can cause substantial power loss at the material surface. Refer to “Mechanical Maintenance” for guidance.
Third Check: Cooling System. Is your chiller operating at the correct temperature? Check the water flow and ensure no kinks in the tubes. An overheating laser tube will drastically reduce power output.
Fourth Check: Laser Tube Health. If all else fails, and your tube is older, it might be degrading and losing power. This requires professional diagnosis or replacement.
Inconsistent Cuts or Etches (Varying Depth/Quality): This often points to problems with beam consistency or focal issues.
First Check: Material Flatness. Ensure the material is perfectly flat on the bed. Warped materials will be out of focus in certain areas, leading to inconsistent results. Use magnets or clamps to flatten if needed.
Second Check: Focal Length. Confirm your laser is properly focused on the material’s surface. Recalibrate your focal distance if necessary.
Third Check: Lens Quality. Inspect your focusing lens for cracks, pitting, or severe haziness that cannot be cleaned. A damaged lens will produce a distorted or inconsistent beam.
Fourth Check: Air Assist. Ensure your air assist is properly functioning and directed at the point of engraving. Insufficient air assist can lead to excessive flare-up and inconsistent material removal.
Distorted or Inaccurate Engravings/Cuts (Geometric Anomalies): These are almost always mechanical issues.
First Check: Loose Belts. Inspect timing belts for proper tension. Slack belts can lead to backlash or skipped steps, causing wavy lines, incorrect dimensions, or ghosting.
Second Check: Dirty/Unlubricated Rails. Check linear rails and bearings. Friction or debris can cause jerky movement and positional inaccuracies. Clean and lubricate as per “Mechanical Maintenance.”
Third Check: Loose Pulleys/Couplings. Ensure all pulleys on stepper motor shafts and along the gantry are securely fastened. Worn or loose couplings between the motor and lead screw can also introduce play.
Fourth Check: Motor Issues. Though less common, a faulty stepper motor or driver can cause erratic movement. This typically requires professional diagnosis.
By approaching issues systematically and understanding the interconnectedness of cleaning, mechanical integrity, and precise settings, users can quickly diagnose and resolve most laser engraving problems. This proactive and informed approach ensures your machine consistently performs at its best, maximizing uptime and production quality.
Conclusions
Regular and thorough maintenance of your laser engraver is an investment that pays dividends in longevity, precision, and consistent quality of your work. By following these guidelines, you can significantly reduce downtime, avoid costly repairs, and keep your laser machine operating at its best for years to come. Ultimately leading to improved project outcomes and increased productivity.
FAQ
Q: Why is regular maintenance so important for a laser engraver?
A: Regular maintenance is crucial because it directly contributes to the longevity, accuracy, and overall performance of the machine. It prevents component degradation, ensures consistent output quality, minimizes operational costs, and safeguards your investment by extending the machine’s operational lifespan and preventing unexpected breakdowns.
Q: What are the most critical components to clean in a laser engraver?
A: The most critical components to clean are the optical elements, specifically the laser lenses and mirrors. Even microscopic dust or residue can scatter or absorb laser energy, leading to reduced beam intensity, uneven engraving, or permanent damage to the optics. The exhaust system and work area (honeycomb bed) are also vital for overall performance and safety.
Q: How often should I lubricate the moving parts of my laser engraver?
A: The frequency of lubrication depends on usage and environmental factors. A general guideline is every 100-200 hours of operation or monthly for heavy users. Always clean the rails thoroughly before applying a specialized lubricant designed for linear motion systems, and avoid general-purpose oils like WD-40.
Q: What causes inconsistent cuts or etchings, and how can I troubleshoot it?
A: Inconsistent cuts or etchings often point to problems with beam consistency or focal issues. Start by checking if the material is perfectly flat, then confirm your laser is properly focused. Inspect your focusing lens for damage, and ensure your air assist is functioning correctly. These steps address the most common causes of inconsistency.
blockquote class="wp-block-quote">Q: Can environmental factors affect my laser engraver’s performance?
A: Yes, environmental factors like temperature and humidity can significantly impact performance. CO2 laser tubes perform optimally within a specific temperature range (typically 18-25°C or 65-77°F for cooling water). Incorrect temperatures can reduce power output or cause condensation. High humidity can affect optics and alter material engraving characteristics. Maintaining a stable, climate-controlled environment is highly beneficial.
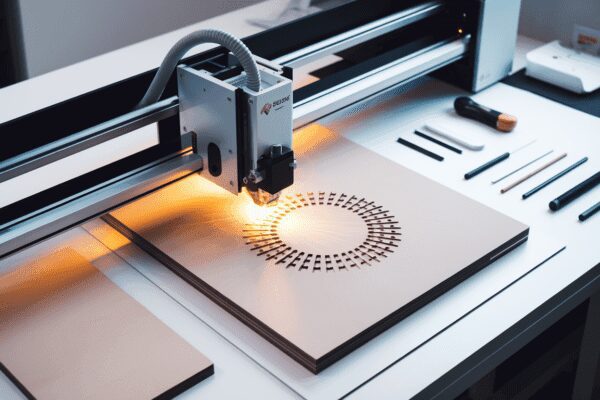
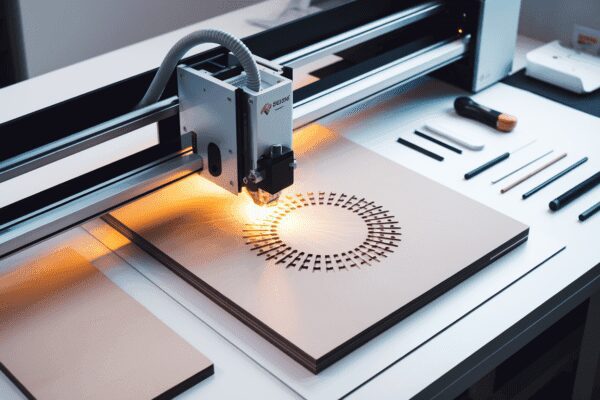
Subscribe to Our Newsletter
And enjoy FREE Download Files, SALE Alerts and Inspiring TIPS
A Guide to Crafting a Personalized Charcuterie Board
A Guide to Crafting the Perfect Personalized Charcuterie Board
Crafting Personalized Memories: A Guide to Laser Cut Picture Frames
[Free Download] Wild Bear Chef Charcuterie Board Engraving File | PNG …
$6.00Original price was: $6.00.$0.00Current price is: $0.00.Free Download
Valentine Love Captions: 6 Charcuterie Board Engraving Files…
$12.00Original price was: $12.00.$7.20Current price is: $7.20.(40% off)
[Free Download] Highland Cow Chef Charcuterie Board Engraving File | P…
$6.00Original price was: $6.00.$0.00Current price is: $0.00.Free Download
[Free Download] Family Quote Charcuterie Board Engraving | PNG Downloa…
$5.00Original price was: $5.00.$0.00Current price is: $0.00.Free Download