Estimated reading time: 15 minutes
Key Takeaways
- Regular maintenance of all components (laser source, optics, mechanical parts) is crucial for longevity and consistent performance across CO2, fiber, and diode laser engravers.
- Optical components (lenses, mirrors) are highly sensitive and require frequent, specialized cleaning to prevent power loss and damage.
- Environmental control (temperature, humidity, dust) significantly impacts machine health and output quality, preventing premature wear and electronic issues.
- Precise calibration (optical alignment, focus, mechanical steps) ensures accuracy, efficiency, and high-quality results.
- A structured preventative maintenance schedule combined with diligent record-keeping is vital for predicting issues, optimizing performance, and maximizing machine lifespan.
Table of Contents
- Understanding Laser Engraver Components and Their Maintenance Needs
- Routine Cleaning and Inspection for CO2 and Fiber Laser Engravers
- Advanced Maintenance Techniques and Troubleshooting for Diode Lasers
- Optimizing Performance Through Environmental Control and Calibration
- Preventative Maintenance Schedule and Record Keeping
- Conclusions
Maintaining your laser engraving machine is crucial for ensuring its longevity, accuracy, and consistent performance. Regular upkeep not only prevents costly repairs but also guarantees the quality of your engraved products. This guide provides essential maintenance tips for various laser engraver types, helping you achieve optimal results every time.
Understanding Laser Engraver Components and Their Maintenance Needs
To ensure optimal performance and longevity of your laser engraver, it’s crucial to understand its core components and their specific maintenance requirements. Regardless of whether you operate a CO2, fiber, or diode laser, proper care of these internal systems directly translates to consistent engraving quality and reduced downtime. This chapter delves into the key components of each laser type and outlines detailed maintenance practices for each.
Laser Tubes (CO2 Lasers)
At the heart of a CO2 laser engraver lies the laser tube, typically a glass tube filled with a mixture of gases. This tube generates the laser beam that performs the engraving. The primary maintenance concern for CO2 laser tubes is efficient cooling. Overheating can significantly reduce the tube’s lifespan and output power. This necessitates maintaining the proper temperature of the water used in the chiller system. Regular inspection of the chiller for proper water levels, coolant purity, and pump functionality is paramount. The water should be distilled to prevent mineral buildup inside the laser tube, which can impede cooling and even cause tube failure. Additionally, periodically flushing the cooling system and replacing the distilled water (or recommended coolant) according to the manufacturer’s guidelines prevents algae growth and mineral deposits. Dust accumulation on the laser tube itself should also be avoided, as it can act as an insulator, leading to increased operating temperatures. Gentle cleaning with a soft, lint-free cloth, when the machine is powered off and cooled, is recommended. A well-maintained cooling system directly extends the operational life of your CO2 laser tube, a significant investment in your machine.
Fiber Laser Sources (Fiber Lasers)
Fiber laser engravers utilize a different mechanism for laser generation, employing an optical fiber doped with rare-earth elements. Unlike CO2 tubes, fiber laser sources are typically enclosed and require less direct user interaction for internal maintenance. However, their longevity heavily relies on a stable operating environment. Maintaining a clean and temperature-controlled workspace is crucial to prevent dust and humidity from entering the sealed enclosure of the laser source, which could compromise internal optics or electronic components. While direct cleaning of the internal fiber elements is not a user task, ensuring proper airflow around the laser source and preventing heat buildup through efficient ventilation systems is vital. Any signs of reduced power output or erratic behavior from a fiber laser source usually indicate an internal issue requiring professional servicing, as user attempts at repair can cause irreparable damage.
Diode Laser Modules (Diode Lasers)
Diode lasers, often found in more compact and affordable engravers, generate their laser beam from semiconductor diodes. Their primary maintenance focus revolves around heat dissipation and lens cleanliness. Diode modules generate a significant amount of heat during operation, and effective cooling is essential to prevent degradation of the diode and maintain consistent power output. Ensure cooling fans are free of dust and debris, and that heatsinks are clear. Regularly inspect and clean the cooling fins if accessible. The focusing lens on diode modules is also susceptible to dust and smoke residue buildup, which can scatter the laser beam, reduce engraving efficiency, and even damage the lens itself. Gentle cleaning of the lens with specialized lens cleaning solutions and lint-free cloths is crucial. Avoid abrasive materials or excessive pressure, which can scratch the delicate lens surface.
Optics (All Laser Types)
The optical system of any laser engraver consists of mirrors and lenses that guide and focus the laser beam onto the material. These components are extremely sensitive to contamination. Dust, smoke residue, and other airborne particles can accumulate on their surfaces, causing the laser beam to lose power, burn inconsistently, or even damage the optics through localized heat buildup. Regular inspection and cleaning of all mirrors and the focus lens are non-negotiable. Only use specialized optical cleaning solutions and lint-free optical wipes. Never touch the optical surfaces with bare hands, as skin oils can leave residues. The frequency of cleaning depends on the engraving materials and the volume of work, but a daily or weekly check is a good practice. Proper alignment of the mirrors is also crucial for CO2 lasers to ensure the beam travels efficiently and focuses accurately. While initial alignment is factory-set, impacts or vibrations can sometimes necessitate re-alignment, a procedure typically reserved for experienced users or technicians.
Mechanical Parts (All Laser Types)
The mechanical components of a laser engraver, including the gantry system, rails, belts, and bearings, are responsible for precise movement of the laser head. These parts are subject to wear and tear and require regular lubrication and cleaning to ensure smooth, accurate, and consistent movement. Dust, debris, and engraving residue can accumulate on rails and bearings, causing friction, reducing accuracy, and even leading to premature component failure. Regularly clean the linear rails and bearings with a lint-free cloth and apply appropriate lubricants as recommended by the manufacturer. Avoid using greases or oils not specified for laser engraver components, as they can attract more dust or damage certain materials. Inspect belts for tension and wear; loose or worn belts can lead to inaccurate engraving and ghosting. Some machines may have lead screws that also require periodic lubrication. The bed and extraction grill should also be regularly cleaned to prevent residue buildup that could interfere with material placement or fume extraction. A well-maintained mechanical system ensures repeatable and high-quality engraving results over the long term.
Routine Cleaning and Inspection for CO2 and Fiber Laser Engravers
Maintaining peak performance in CO2 and fiber laser engravers hinges on establishing and adhering to a consistent regimen of cleaning and inspection. This routine maintenance is crucial not only for preserving beam quality and power but also for extending the lifespan of costly components. By proactively addressing potential issues, you can prevent unexpected downtime and ensure your machine operates at its highest efficiency.
Cleaning Lenses and Mirrors (CO2 and Fiber Lasers)
The optical components – lenses and mirrors – are perhaps the most critical elements demanding regular cleaning. In CO2 lasers, there are typically three mirrors (one at the back of the tube, two redirecting the beam within the gantry) and a focusing lens in the laser head. Fiber lasers, while having a more enclosed beam path, still have a protective window and a focusing lens that require meticulous attention. Residues from engraving, such as smoke, vaporized material, and dust, can accumulate on these surfaces, causing the laser beam to scatter, lose power, and potentially overheat the optics, leading to permanent damage. Loss of beam power often manifests as incomplete cuts or faint engravings.
For CO2 lasers, cleaning typically involves:
- Powering down the machine and ensuring it is completely de-energized and cooled.
- Carefully removing the focus lens from its housing using specialized tools (if required by the manufacturer), ensuring not to scratch or drop it.
- Using only optical-grade lens cleaning solution (e.g., isopropyl alcohol 99.9% pure or methanol, specifically formulated for optics) and lint-free optical wipes or swabs. Apply a few drops of solution to a fresh wipe, then gently wipe the lens surface in a circular motion from the center outwards, or in a straight line for mirrors, using a new section of the wipe for each pass to avoid re-depositing contaminants.
- Inspect the optics under a bright light for any remaining streaks or particles. Repeat the cleaning process if necessary.
- Replace the lens and mirrors carefully, ensuring they are oriented correctly.
For fiber lasers, the accessible cleaning points are typically the protective window (if present) and the focusing lens. The internal optics are usually sealed. The cleaning procedure is similar to that for CO2 optics, using appropriate optical cleaning solutions and wipes. It is important to consult your machine’s manual, as some fiber laser protective windows might require specific cleaning agents to avoid damaging special coatings.
Inspecting and Cleaning the Laser Tube (CO2 Lasers)
While you won’t directly clean the inside of a CO2 laser tube, external inspection and maintenance are vital. Regularly check the exterior of the glass tube for any signs of cracks, discoloration, or water leaks. Ensure the electrical connections to the tube are secure and free from corrosion. More importantly, focus on the integrity of the cooling system. Verify that the water circulates freely and there are no kinks in the hoses. Inspect the chiller or water pump for proper operation, ensuring the water temperature remains within the manufacturer’s specified range. The cooling water itself should be clear and free of debris, algae, or cloudiness. If the water appears contaminated, a full flush and refill with distilled water (and appropriate anti-algae additives if recommended) is necessary to prevent internal tube degradation. Dust accumulation on the exterior of the tube and connecting wires should be gently removed with a soft cloth or compressed air, as dust can act as an insulator and impede heat dissipation.
Inspecting Belts, Rails, and Moving Parts (CO2 and Fiber Lasers)
The mechanical accuracy of your laser engraver is paramount for consistent, high-quality results. The gantry system, which moves the laser head, relies on a combination of linear rails, bearings, drive belts, and sometimes lead screws.
- Belts: Inspect all drive belts (X and Y axes) for proper tension. They should be taut but not overly tight. Overly loose belts can lead to backlash, “ghosting” (duplicate lines), or inaccurate positioning. Sagging belts are a clear sign of looseness. Check for any signs of wear, fraying, cracking, or missing teeth. Worn belts should be replaced promptly.
- Rails and Bearings: Linear rails and their corresponding bearings guide the laser head smoothly across the engraving area. These surfaces are prone to accumulating dust, debris, and engraving residue, which can cause friction, jerky movements, and reduce accuracy. Routinely clean these rails with a lint-free cloth, removing any visible grime. After cleaning, apply a thin layer of manufacturer-recommended lubricant to the rails (or the bearings if specified). Avoid over-lubricating, as excessive lubricant can attract more dust.
- Gantry and Cables: Ensure that the gantry moves freely and smoothly without any binding or excessive resistance when manually pushed (with power off). Inspect all cables trailing the laser head or gantry for any signs of wear, pinching, or damage. Damaged cables can lead to intermittent operation or electrical shorts.
By diligently performing these cleaning and inspection routines, you significantly contribute to the overall health and performance of your laser engraver, minimizing costly repairs and ensuring a consistent output of high-quality engravings.
Advanced Maintenance Techniques and Troubleshooting for Diode Lasers
While diode lasers are often lauded for their “set it and forget it” simplicity compared to CO2 systems, effective long-term performance still demands advanced maintenance techniques and a proactive approach to troubleshooting. Unlike the complex mirror alignments of CO2 lasers, diode lasers typically have a fixed beam path after generation, but internal optical elements and power delivery systems are critical to their output and longevity. Ignoring these aspects can lead to diminished power, inconsistent engraving, and premature module failure.
Checking and Adjusting Optical Alignment (Internal Diode Module Focus)
For most diode laser engravers, there isn’t an “alignment” of multiple mirrors as seen in CO2 systems. Instead, the critical optical alignment within a diode laser module refers primarily to the precise positioning of internal lenses that shape and focus the raw laser output from the diode itself. The user-adjustable component is typically the focus lens, which moves along the Z-axis to converge the beam to its smallest point on the material. However, some higher-end diode modules might have internal, factory-set focusing optics that, if disturbed, can drastically impact beam quality. While user adjustment of these internal optics is generally not recommended or even possible without specialized tools, understanding their critical role is important for advanced troubleshooting.
A perfectly focused laser beam is paramount for both precision and efficiency. When the internal optical alignment is sub-optimal, or if the external focusing lens is dirty or mispositioned, the laser spot will be larger, less intense, and shaped irregularly. This results in: Reduced Engraving Power: A larger spot size means the same laser power is spread over a wider area, thus reducing the power density and making the laser less effective at cutting or engraving. Lack of Detail: Fine lines and intricate designs will appear blurry or jagged, as the laser can’t achieve the required precision. Slow Engraving/Cutting Speeds: To compensate for the reduced power density, you’ll need to run the laser slower or at higher power settings, which reduces throughput and shortens the diode’s lifespan. Uneven Results: If the beam is not uniformly focused across its diameter, parts of your engraving might be deeper or darker than others.
To check the focus, run a focus test pattern (e.g., a ramp test or a series of lines at varying Z heights) on a scrap piece of material. The sharpest, thinnest line or dot indicates optimal focus. While the primary focus adjustment is usually manual (turning a ring on the laser head), ensuring the lens is clean and seated correctly is part of maintaining this “alignment.” If you suspect internal optics are misaligned (e.g., after an impact or if the unit was tampered with), and cleaning the external lens doesn’t resolve the issue, the diode module itself might need professional recalibration or replacement. This is less a user maintenance task and more a diagnostic one that informs a repair decision.
Troubleshooting Common Issues: Laser Diode and Power Delivery
Many performance issues with diode lasers can be traced back to the diode module itself or the way power is supplied to it.
- Diminished Laser Output or No Laser Light:
- Check Power Connections: Ensure all power cables from the power supply to the controller board, and from the controller board to the diode module, are securely connected. Loose connections can lead to intermittent power or no power at all. Inspect for any frayed or damaged wires.
- Power Supply Health: Test the output voltage of the power supply unit (PSU) if you have a multimeter and know how to safely use it. An under-performing PSU can starve the diode of the necessary voltage and current, leading to reduced output. If the PSU is failing, it will need replacement.
- Driver Circuitry: The diode module often contains a driver circuit that regulates the current to the laser diode. If this circuit fails, the diode won’t fire or will fire weakly. This usually necessitates replacing the entire diode module, as these circuits are typically integrated.
- Diode Overheating: Diode lasers are very sensitive to heat. Ensure the fan on the diode module is operating correctly and is free from dust and debris. If the fan is failing or airflow is obstructed, the diode will quickly overheat, leading to thermal shutdown or permanent damage and reduced power. Some diode modules have built-in thermal protection that reduces power or shuts down when overheating occurs. This often manifests as the laser starting strong but quickly fading.
- Dirty Protective Window/Lens: As discussed in the previous section, even a slight film of residue on the protective window or focusing lens can significantly absorb laser power. Clean these thoroughly with optical-grade wipes and solution.
- Inconsistent Engraving (Patchy, Uneven):
- Unstable Power Supply: Fluctuations in the input power to the laser can cause inconsistent engraving. This points back to the PSU or potentially issues with the electrical outlet.
- Loose Connections: Any loose electrical connection on the signal lines (PWM/TTL) from the controller to the diode module can cause the laser to fire erratically or with varying intensity.
- Overheating: As mentioned, an overheating diode will often reduce its power output as a self-preservation mechanism, leading to uneven engraving as it cycles through thermal regulation.
- Compromised Diode: If the diode has been operated consistently at too high a temperature or beyond its specified power limits, its internal structure can degrade, leading to permanent power loss and inconsistent output across its emission area. In such cases, the diode module needs replacement.
- No Laser Light, but Fan is Running: This suggests the power is reaching the module, but the laser diode itself or its internal driver circuit is not functioning. This is a strong indicator of an internal module failure. Check your software settings to ensure the laser output is enabled and the power value is not set to zero.
By systematically troubleshooting these common issues, often starting with the simplest checks like connections and cleanliness, you can diagnose and resolve most performance problems with your diode laser. Understanding the interplay between power delivery, thermal management, and basic optics is key to maintaining a diode laser at its peak performance.
Optimizing Performance Through Environmental Control and Calibration
Beyond regular cleaning and component-specific maintenance, the operational environment and precise calibration are paramount in achieving and sustaining optimal laser engraving performance. Overlooking these aspects can lead to erratic results, premature component failure, and a substantial increase in maintenance demands. A controlled environment safeguards your investment, while diligent calibration ensures consistent, high-quality output.
The Impact of Environmental Factors
Laser engravers are precision instruments, and their performance is highly susceptible to the surrounding environment. Controlling temperature, humidity, and dust levels directly translates to reduced wear and tear, improved accuracy, and extended machine lifespan.
- Temperature: Extreme temperatures, particularly heat, are detrimental to laser engravers. High ambient temperatures can stress power supplies, electronic components, and especially laser sources. For CO2 lasers, the cooling system (chiller) works harder to maintain optimal laser tube temperature, leading to increased wear on the chiller and potential thermal throttling of the laser tube itself if its cooling capacity is exceeded. Fiber laser sources and diode modules also generate heat internally, and if the surrounding air is already hot, their cooling mechanisms become less effective, risking component degradation and reduced output power. Conversely, very low temperatures can cause components to become brittle or affect the viscosity of lubricants, hindering mechanical movement. Maintaining a stable room temperature, ideally between 65°F and 75°F (18°C and 24°C), is crucial.
- Humidity: High humidity is a silent killer for electronic devices. Moisture can condense on critical electronic components, leading to short circuits, corrosion, and premature failure. It can also cause problems with optical components by leaving behind water spots and encouraging dust adherence when it dries, potentially even leading to mold growth on neglected surfaces. Furthermore, very low humidity can increase static electricity, which poses a risk to sensitive electronics. An ideal humidity range for most laser engravers is between 40% and 60% relative humidity. Using a dehumidifier in humid environments or a humidifier in excessively dry climates can mitigate these risks.
- Dust and Particulates: This is perhaps the most obvious environmental threat. Dust, wood particles, resin fragments, and other airborne debris generated during engraving can settle on every surface of the machine. On optical components (lenses, mirrors, protective windows), dust immediately reduces laser transmission efficiency, causing power loss and potential localized overheating that can permanently damage the optics. On mechanical components (rails, bearings, belts), dust acts as an abrasive, accelerating wear and tear, leading to inaccurate movements, increased friction, and ultimately component failure. Dust can also clog cooling fins on laser modules and power supplies, hindering heat dissipation. Maintaining a clean workspace, ideally one separated from heavy woodworking or grinding operations, is critical. Employing air purification systems, ensuring efficient exhaust ventilation, and regularly wiping down surfaces are preventative measures. Covering the machine when not in use can also significantly reduce dust accumulation.
Importance of Regular Calibration and Optical Alignment
Calibration is a methodical process of fine-tuning your laser engraver’s systems to ensure it performs accurately and consistently. While some aspects of calibration are performed at the factory, environmental changes, wear and tear, and even minor jostling can cause settings to drift.
- Optical Alignment (CO2 Lasers): This is arguably the most critical calibration for CO2 engravers. It involves ensuring the laser beam travels precisely through the center of all mirrors and the focus lens, striking the material exactly where intended. Misalignment can manifest as:
- Reduced power at the engraving surface.
- Inconsistent cutting or engraving depth across the bed.
- Offset engraving, where the actual engraving doesn’t match the design’s intended position.
- Damage to mirrors or lens housings due to the beam hitting their edges.
Proper alignment ensures maximum power transmission, a perfectly round and consistent beam spot, and accurate positioning. This typically involves firing short test pulses at indicator paper or tape on specific points to assess the beam’s path and making minute adjustments to mirror mounts. This is a delicate process and, if unfamiliar, should initially be performed with reference to the machine manual or under the guidance of an experienced technician.
- Focus Calibration: While touched upon in previous chapters, precise focus calibration is a continuous requirement. The exact focal distance can slightly vary due to material thickness, lens type, and even temperature fluctuations affecting material expansion. Regularly calibrating your focus (e.g., via a ramp test) ensures the laser beam is always at its smallest, most intense point on the material surface for optimal cutting and engraving efficiency.
- Mechanical Calibration (Steps Per Millimeter): Over time, or due to belt stretch/wear, the motors might not translate to exact physical distances. Calibrating the “steps per millimeter” for your X and Y axes ensures that a command to move 100mm actually moves the laser head precisely 100mm. This is vital for dimensional accuracy in designs. This calibration typically involves engraving a precisely measured square or line and then adjusting software settings based on the measured deviations.
- Power Calibration and Material Settings: While not a mechanical calibration, maintaining a robust library of calibrated power and speed settings for various materials is a form of performance optimization. As laser tubes age or as environmental conditions change, slight adjustments to these settings might be necessary to achieve consistent results. Regularly testing and updating these settings ensures predictable outcomes and efficient material processing.
By diligently managing the environmental factors surrounding your laser engraver and committing to a schedule of regular calibration, you are not just performing maintenance; you are actively optimizing your machine for long-term reliability, precision, and the highest quality output possible.
Preventative Maintenance Schedule and Record Keeping
Establishing a robust preventative maintenance schedule and rigorously adhering to it is the cornerstone of optimal laser engraver performance and longevity. Without a structured plan, maintenance often becomes reactive, addressing problems only after they occur, leading to costly downtime and inconsistent results. This chapter outlines a comprehensive schedule tailored for different laser types and underscores the immense value of diligent record-keeping.
Crafting a Preventative Maintenance Schedule
A preventative maintenance schedule should be a living document, tailored to your specific machine, usage frequency, and operating environment. The intervals provided below are general guidelines and should be adjusted based on your experience and manufacturer recommendations.
- Daily/Before Each Use (All Laser Types):
- Inspect optics (lenses and mirrors/protective window) for visible dust or debris. Clean if necessary.
- Check for any unusual noises during machine startup or movement.
- Verify exhaust system is functioning correctly (airflow, fan noise).
- For CO2 lasers: Check chiller water level, temperature, and ensure proper circulation.
- For diode lasers: Ensure cooling fan on module is operational and intake/exhaust vents are clear.
- Quick visual inspection of gantry, rails, and belts for debris.
- Clean the engraving bed surface if materials were placed directly on it.
- Weekly (or after 20-40 operating hours, whichever comes first):
- All Laser Types:
- Thorough cleaning of all accessible optics (lenses, mirrors, protective windows).
- Clean linear rails, gantry, and lead screws (if applicable).
- Inspect belts for tension and wear. Adjust or replace if needed.
- Clean the engraving bed, honeycomb, or slat bed thoroughly to remove accumulated debris.
- Wipe down the entire machine exterior to remove dust and residue.
- Check that all wiring and connections are secure and free from damage.
- CO2 Lasers Specific:
- Check CO2 laser tube for any external signs of wear or discoloration.
- Inspect cooling hoses for kinks, leaks, or degradation.
- Test chiller alarm functions (if applicable).
- Diode Lasers Specific:
- Inspect cooling fan blades for dust buildup and clean gently.
- Ensure heatsink fins are clear of obstruction.
- All Laser Types:
- Monthly (or after 80-160 operating hours):
- All Laser Types:
- Lubricate linear rails, bearings, and lead screws with manufacturer-recommended lubricants.
- Deep clean the entire interior of the machine, removing all dust and debris.
- Inspect all rollers and bearings for smooth operation and signs of wear.
- Check condition of all accessible cables for cracking, chafing, or signs of heat.
- CO2 Lasers Specific:
- Flush and replace distilled/de-ionized water (or recommended coolant) in the chiller system, if manufacturer recommends monthly change. Inspect for algae growth.
- Clean the chiller’s radiator fins to ensure efficient heat exchange.
- Perform a visual inspection of the beam path, checking for any signs of beam scatter or misdirection.
- Check the integrity of the exhaust hoses and clean any accessible sections to remove tar/creosote buildup.
- Fiber Lasers Specific:
- Inspect and clean the exhaust fan and filter (if present on the laser source enclosure).
- Check environmental controls around the fiber laser source for optimal temperature and humidity.
- All Laser Types:
- Quarterly/Bi-Annually (or after 250-500 operating hours):
- All Laser Types:
- Thorough physical inspection of the entire machine for loose fasteners, structural integrity, and unusual wear.
- Re-calibrate X and Y axis steps-per-millimeter (mechanical calibration).
- Calibrate focus if there are any doubts about accuracy.
- Consider replacing common wear parts like belts if showing significant signs of fatigue, even if not critically failed.
- CO2 Lasers Specific:
- Perform a full optical alignment check and adjustment (if necessary and you are trained).
- Consider a more thorough chiller maintenance, including a professional cleaning or filter replacement.
- Test emergency stop buttons and safety interlocks.
- All Laser Types:
- Annually (or after 1000-2000 operating hours):
- All Laser Types:
- Consider professional servicing for a comprehensive inspection and tune-up.
- Evaluate major component wear (laser source health, power supply stability, motor integrity).
- Replace all consumables due for end-of-life (e.g., air filter elements for external air assist pumps).
- Review and update your maintenance schedule based on the past year’s observations.
- All Laser Types:
The Invaluable Role of Diligent Record-Keeping
A meticulously maintained logbook or digital record of all maintenance activities is as important as the maintenance itself. This record should include:
- Date of Maintenance: When the activity was performed.
- Component/Area Maintained: What was cleaned, inspected, or replaced.
- Details of Activity: Specific steps taken, observations made (e.g., “mirror 3 had heavy soot buildup,” “belt tension loose on Y-axis”).
- Parts Replaced: List of new components installed (e.g., “new focus lens,” “Y-axis belt”).
- Technician/Operator: Who performed the maintenance.
- Machine Hours/Usage: Current operating hours or days since last maintenance.
- Performance Observations (Before/After): Any noticeable changes in machine performance or engraving quality.
The benefits of diligent record-keeping are numerous:
- Tracking Wear and Tear: Identifies which components wear out fastest, allowing for proactive stocking of spare parts and more accurate forecasting of replacement needs.
- Predictive Maintenance: By noting recurring issues (e.g., a specific mirror frequently getting dirty), you can deduce underlying problems (e.g., inadequate exhaust, poor air assist) or predict when a component might fail.
- Troubleshooting Aid: When a problem does arise, the maintenance log provides a history of actions taken, helping to narrow down potential causes and expedite diagnosis.
- Warranty Compliance: Many manufacturers require proof of regular maintenance for warranty claims.
- Optimizing Maintenance Intervals: Over time, your records will reveal the true lifespan of components in your specific operating environment, allowing you to fine-tune your schedule for maximum efficiency.
- Long-Term Value Preservation: A detailed maintenance history increases the resale value of your machine, providing prospective buyers with confidence in its upkeep.
- Operational Efficiency: By preventing unexpected breakdowns and ensuring peak performance, a well-structured maintenance plan directly contributes to uninterrupted workflow and consistent, high-quality output.
In essence, preventative maintenance is an investment, not an expense. When combined with thorough record-keeping, it transforms maintenance from a reactive chore into a strategic tool for maximizing the lifespan, reliability, and precision of your laser engraving machine.
Conclusions
Proper maintenance is the cornerstone of efficient and reliable laser engraving. By consistently implementing the recommended cleaning, inspection, and calibration procedures, you can significantly extend the life of your equipment, enhance engraving quality, and avoid unexpected downtime. Invest time in maintenance to safeguard your laser engraving business.
FAQ
Q: Why is regular maintenance important for a laser engraving machine?
A: Regular maintenance is crucial for ensuring the machine’s longevity, accuracy, and consistent performance. It prevents costly repairs, guarantees product quality, and avoids unexpected downtime.
Q: What are the primary maintenance concerns for CO2 laser tubes?
A: The main concern for CO2 laser tubes is efficient cooling to prevent overheating, which can reduce lifespan and power. This involves maintaining proper chiller water levels, purity, temperature, and regularly flushing the system.
Q: How often should I clean the optics (lenses and mirrors) on my laser engraver?
A: The frequency depends on engraving materials and work volume, but a daily or weekly check is good practice. Always use specialized optical cleaning solutions and lint-free wipes, and avoid touching surfaces with bare hands.
Q: What environmental factors can impact my laser engraver’s performance?
A: Temperature (ideally 65-75°F/18-24°C), humidity (40-60% RH), and dust levels significantly affect performance. Extreme temperatures, high humidity, and dust accumulation can lead to component stress, corrosion, and reduced accuracy.
Q: What is the benefit of keeping a detailed maintenance logbook?
A: A maintenance logbook helps track wear and tear, predict component failures, aid in troubleshooting, ensure warranty compliance, optimize maintenance intervals, preserve machine resale value, and contribute to overall operational efficiency.
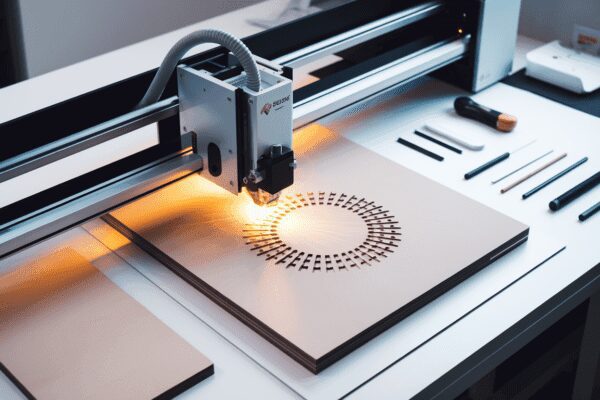
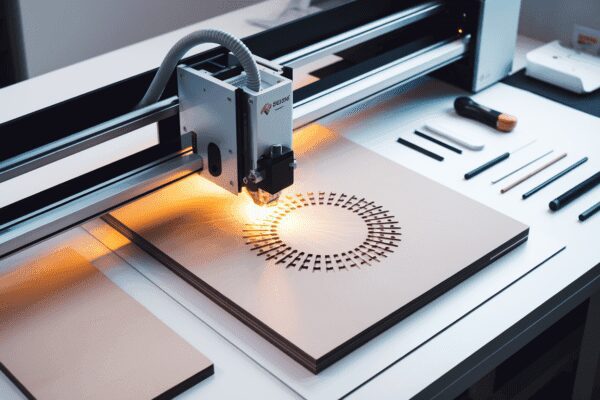
Subscribe to Our Newsletter
And enjoy FREE Download Files, SALE Alerts and Inspiring TIPS
How to Create Stunning Engraved Slate Coasters
How to Create Stunning Engraved Slate Coasters
A Guide to Creating the Perfect Engraved Charcuterie Board
[Free Download] Wild Bear Chef Charcuterie Board Engraving File | PNG …
$6.00Original price was: $6.00.$0.00Current price is: $0.00.Free Download
[Free Download] Tiger Chef 3D Illusion Charcuterie Board Engraving | P…
$6.00Original price was: $6.00.$0.00Current price is: $0.00.Free Download
Valentine Love Captions: 6 Charcuterie Board Engraving Files…
$12.00Original price was: $12.00.$7.20Current price is: $7.20.(40% off)
American Eagle Flag Laser Engraving File for Charcuterie & Cutting…
$6.00Original price was: $6.00.$3.90Current price is: $3.90.(35% off)