Estimated reading time: 7 minutes
Key Takeaways
- 3D laser engraving transforms materials by varying laser depth based on grayscale images (depth maps) to create tactile, textured reliefs.
- Successful 3D engraving hinges on meticulous material preparation (sanding, cleaning, masking) and high-quality digital files (high resolution, 8-bit grayscale, lossless formats).
- Mastering machine and software settings, particularly maximum power, speed, and DPI, is crucial; always use a test grid and ensure precise laser focus.
- The technique encompasses both 3D photo engraving, which creates literal physical depth, and 3D illusion engraving, which uses optical tricks for perceived depth.
- Consistent testing and understanding the interplay of settings are paramount for achieving professional, repeatable 3D engraving results.
Table of Contents
- Understanding the Basics of 3D Illusion Laser Engraving
- Preparing Your Materials and Files
- Mastering Machine and Software Settings
- Conclusions
- Frequently Asked Questions
Dive into the fascinating world of 3D laser engraving. This article will guide you through the techniques to add depth and dimension to your projects, transforming flat surfaces into intricate works of art. We’ll explore everything from material preparation to software settings, helping you master this advanced engraving method and create impressive pieces.
Understanding the Basics of 3D Illusion Laser Engraving
While standard 2D engraving simply etches a design onto a material’s surface, much like drawing with a pen, 3D laser engraving fundamentally transforms the material itself. It is a process of digital sculpting, where the laser beam removes material at varying depths to create a tangible, textured relief. Instead of a flat image, you get a physical topography that you can both see and touch. This is not a simple outline or fill; it’s a true three-dimensional effect carved directly into the substrate, making it a powerful technique for creating high-value, detailed products. The key to this process lies not in the laser’s path alone, but in its ability to modulate its power dynamically based on digital image information.
From Grayscale to Physical Relief
The foundation of 3D laser engraving is the interpretation of a grayscale image, often referred to as a depth map. Your laser software translates the brightness value of each pixel in the image into a specific power output for the laser. This relationship is direct and intuitive:
- Pure White (Value 255): The laser fires at its lowest power setting, or not at all. This leaves the material’s surface untouched or only slightly marked, creating the highest points of the relief.
- Pure Black (Value 0): The laser fires at its maximum programmed power. This ablates or vaporizes the most material, creating the deepest parts of the engraving.
- Shades of Gray: All the gray values between white and black correspond to a proportional laser power level. A 50% gray pixel will command the laser to fire at half its maximum power, creating a depth halfway between the highest and lowest points.
As the laser head moves back and forth, rastering across the material, it continuously adjusts its power based on the pixel it is currently over. This meticulous process carves the image, pixel by pixel, into a physical object with hills, valleys, and smooth gradients, effectively turning a 2D grayscale image into a 3D tactile surface.
This principle is most clearly demonstrated in 3d photo laser engraving. When a standard photograph is converted to grayscale, an incredible amount of depth information is naturally present. Consider a portrait: the tip of the nose and the forehead, catching the most light, will be the lightest parts of the image. These translate to high points in the engraving. Conversely, the shadows under the chin, the recesses of the eyes, and strands of dark hair will be the darkest parts, which the laser will engrave most deeply. The result is a stunning bas-relief that captures the likeness and form of the subject with photorealistic depth.
Building upon this foundation is the more advanced technique of 3d illusion laser engraving. While 3D photo engraving creates a literal physical relief, illusion engraving combines shallow physical depth with clever optical trickery. This method uses specially prepared digital files—not typically photographs—that incorporate artistic elements like fine lines, crosshatching, and engineered gradients. The laser engraves these patterns, and while the physical depth may be minimal, the way these engraved lines and shadows interact with ambient light fools the human eye. The brain interprets these visual cues and perceives a much greater sense of depth, roundness, and form than is physically present. It’s a synthesis of physical engraving and visual psychology, enabling the creation of designs that appear to pop out from the surface with dramatic, almost holographic, effect.
Preparing Your Materials and Files
A successful 3D engraving is born long before the laser fires; it begins with meticulous preparation of both your physical material and your digital file. The quality of your raw materials directly dictates the fidelity of the final relief. While many materials can be 3D engraved, the process of 3d laser engraving on wood is particularly popular and offers a great case study in proper preparation. Not all woods are created equal for this task. The ideal choice is a hardwood with a fine, consistent grain and uniform density, such as American Cherry, Alder, or Hard Maple. These woods react predictably to the laser, allowing for smooth, gradual depth changes. Woods like oak, with its strong, open grain, or pine, with its varying density between growth rings, will engrave unevenly and obscure fine details. Basswood is another excellent, though softer, option prized for its near-invisible grain, providing a perfect canvas. Once you’ve selected your wood, surface preparation is key:
- Start by sanding the surface perfectly smooth. Work your way up from a medium grit (like 150) to a fine grit (220 or higher) sandpaper. A flawless surface is critical as any imperfection will be noticeable in the final product.
- Thoroughly clean the surface after sanding. Use compressed air or a tack cloth to remove every particle of dust. Dust left on the surface can interfere with the laser beam, causing pitting and marring the engraving.
- Consider applying a layer of transfer mask. This low-tack adhesive paper protects the un-engraved areas from smoke and resin residue, ensuring the highest points of your relief remain clean and bright, which enhances the overall contrast and 3D effect.
Selecting and Preparing Your Digital Blueprint
Just as crucial as the physical workpiece is the digital file that guides the laser. For 3D engraving, this isn’t just any image; it is a specialized depth map. The quality and characteristics of your 3d laser engraving files will make or break the illusion of depth. A superior file is defined by its resolution, its bit depth, and its format. First, resolution must be high—a minimum of 300 DPI (dots per inch) is recommended, with 600 DPI being even better for intricate designs. A low-resolution file will result in visible stepping or pixelation in the slopes of your engraving, ruining the smooth topographical effect. Second is the importance of smooth gradients. Your image must be a true 8-bit grayscale file, which contains 256 distinct shades of gray from pure black to pure white. These shades are what allow the laser to create subtle, flowing changes in depth. An image with harsh, posterized transitions will result in a crude, terraced engraving rather than a realistic relief. For this reason, you should always work with lossless file formats like TIFF, PNG, or BMP. The compression used in JPEG files can introduce artifacts that disrupt these smooth gradients, creating an unwanted mottled texture in your final piece.
Finding and Creating 3D Files
You can find high-quality, pre-made 3D engraving files on various online marketplaces and design communities. Look for files specifically sold as “depth maps” or “grayscale for 3D engraving.” For those who wish to create their own, two primary methods exist. The first is to convert a high-quality photograph into grayscale using image editing software like Adobe Photoshop or GIMP. This requires careful adjustment of brightness and contrast to ensure the light and dark areas accurately represent the desired high and low points. The second, more advanced method, is to use 3D modeling software like Blender or ZBrush. You can sculpt a digital model and then render a “Z-depth pass,” which generates a perfect pixel-for-pixel grayscale depth map based on the true geometry of your 3D model. This technique offers the ultimate control, allowing you to create flawless files for the most stunning and convincing 3D laser engravings.
Mastering Machine and Software Settings
With your prepared material and high-quality depth map in hand, the focus shifts to the machine itself. Translating a digital grayscale file into a physical relief is a delicate dance between laser power, speed, and resolution. Mastering these 3d laser engraving settings is the final, and most critical, technical hurdle. While specific values vary wildly between machines, materials, and designs, the underlying principles are universal. These settings are not a “set it and forget it” affair; they are a triad of variables that you must balance for each unique project. Your main parameters within the laser software will be:
- Power: In 3D engraving mode, you are not setting a single power level. Instead, you are defining the maximum power the laser will use. When the software encounters a pure black pixel in your file, it will command the laser to fire at this 100% setting, creating the deepest point. For a white pixel, it will use 0% of this power. All gray shades in between will receive a proportional power level. The art is in setting a maximum that is high enough to achieve the desired depth in your material but low enough to avoid excessive charring and flaming that can obliterate fine detail.
- Speed: This controls how fast the laser head moves across the material. Speed and power have an inverse relationship. A slower speed allows the laser beam to dwell on a single point for longer, transferring more energy and resulting in a deeper engraving. A faster speed delivers less energy, creating a shallower cut. For 3D engraving, a moderate to slow speed is often preferred to allow the laser enough time to carve out significant depth and accurately render the smooth gradients of the depth map.
- Interval/DPI (Dots Per Inch): This setting determines the spacing between each horizontal pass of the laser, also known as the scan gap. A higher DPI means the lines are closer together (a smaller interval), causing them to overlap. This overlap is crucial for creating a smooth, almost cast-like finish, effectively sanding away the lines between passes. A lower DPI leaves more space between lines, which can result in a ridged, textured finish and faster engraving times. For high-quality 3D photo reliefs, a high DPI of 500 or more is typically required.
The Non-Negotiable Step: The Test Grid
Before you even think of running your final design, you must commit to a testing phase. Settings that created a perfect result on cherry wood will produce a charred mess on basswood. The single most effective way to dial in your parameters is by running a material test grid. This process involves engraving a matrix of small shapes on a scrap piece of the exact same material you plan to use for your project. Create a grid where each row represents a different speed and each column a different power setting. By examining the results, you can visually identify the “sweet spot”—the combination that gives you the best depth, sharpest detail, and least amount of burning. Crucially, before running any test, ensure your laser is perfectly focused. An improperly focused beam is wider and less intense, resulting in mushy, undefined details and negating all your careful file preparation. A sharp focus is paramount for rendering the crisp edges and subtle textures that make a 3D engraving truly stand out. Remember, this testing process isn’t a suggestion; it is a fundamental requirement for achieving professional, repeatable results.
Conclusions
You now have the foundational knowledge to begin your journey with 3D laser engraving. By experimenting with different materials, designs, and settings, you can unlock a new level of creativity. Remember to start with simpler projects, refine your technique, and soon you’ll be producing breathtaking 3D masterpieces that captivate and impress your audience.
Frequently Asked Questions
Q: What is the main difference between 2D and 3D laser engraving?
A: 2D laser engraving etches a flat design onto a surface, like drawing. 3D laser engraving, however, removes material at varying depths based on a grayscale image (depth map) to create a tangible, textured relief with physical topography you can see and touch.
Q: Why is a grayscale image important for 3D laser engraving?
A: A grayscale image, or depth map, is the foundation of 3D engraving. The laser software translates the brightness value of each pixel (from pure white to pure black, and all shades of gray in between) into a specific power output. This allows the laser to create varying depths, forming the 3D relief.
Q: What types of wood are best for 3D laser engraving?
A: Hardwoods with fine, consistent grain and uniform density, such as American Cherry, Alder, or Hard Maple, are ideal. Basswood is also excellent due to its near-invisible grain. Woods with strong or inconsistent grains (like oak or pine) will engrave unevenly and are less suitable for fine 3D details.
Q: What are the critical laser settings for 3D engraving?
A: The three critical settings are Power (which defines the maximum power used for the deepest points), Speed (how fast the laser head moves, affecting depth), and Interval/DPI (spacing between laser passes, crucial for smooth finishes). These must be balanced and tested for each project and material.
Q: Why is running a test grid so important for 3D laser engraving?
A: A test grid is crucial because optimal settings vary widely by machine, material, and design. It allows you to experiment with different power and speed combinations on a scrap piece of your actual material to find the “sweet spot” that yields the best depth, detail, and minimal burning before you engrave your final project.
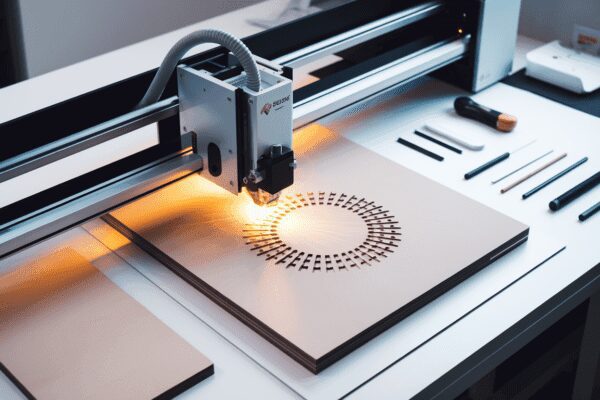
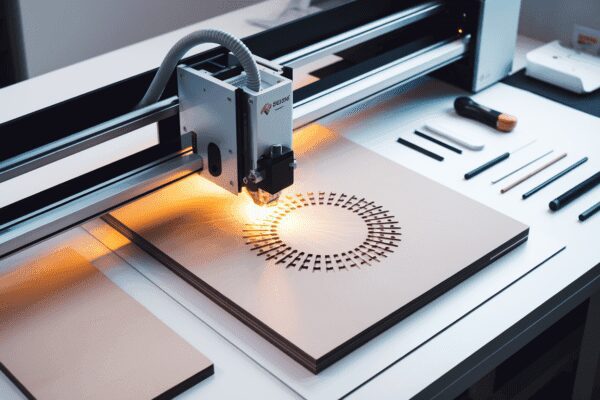
Subscribe to Our Newsletter
And enjoy FREE Download Files, SALE Alerts and Inspiring TIPS
A Guide to Creating the Perfect Engraved Charcuterie Board
Crafting the Perfect Laser Engraved Charcuterie Board
A Guide to Crafting a Personalized Charcuterie Board
[Free Download] Wild Bear Chef Charcuterie Board Engraving File | PNG …
$6.00Original price was: $6.00.$0.00Current price is: $0.00.Free Download
Valentine Love Captions: 6 Charcuterie Board Engraving Files…
$12.00Original price was: $12.00.$7.20Current price is: $7.20.(40% off)
[Free Download] Family Quote Charcuterie Board Engraving | PNG Downloa…
$5.00Original price was: $5.00.$0.00Current price is: $0.00.Free Download
American Eagle Flag Laser Engraving File for Charcuterie & Cutting…
$6.00Original price was: $6.00.$3.90Current price is: $3.90.(35% off)